FCB-1 Operating manual
This is the instruction manual for the FIRGELLI FCB-1 LCD screen control box. The FCB-1 control box is designed to control up to four linear actuators, accommodating both actuators with built-in feedback systems (such as hall or optical sensors) and those without feedback.
When using actuators with built-in feedback, the FCB-1 can synchronize up to four actuators to run at the exact same speed, ensuring precise and coordinated movement. This synchronization capability is particularly useful in applications requiring multiple actuators to operate in unison.
For actuators without built-in feedback, the FCB-1 still offers the ability to control up to four actuators, but without the synchronization feature. Instead, the control box provides timer functions and speed adjustment capabilities for these actuators.
The FIRGELLI FCB-1 LCD screen control box is a state-of-the-art device designed for electric linear actuators, offering advanced control and functionality. Whether you're lifting doors, adjusting desks, or managing uneven loading scenarios, the FCB-1 ensures optimal performance and smooth operation.
BEFORE YOU START
Ensure the DIP switches on the side of the control box are set correctly for the number of actuators you are going to use. There are 3 DIP switches for up to 4 actuators. Up is on and down is off. Here is the switch position for running 1-4 actuators.
- For 1 Actuator - All DIP switches down (off)
- For 2 Actuators - DIP switch 1 on (up), 2&3 down (off)
- For 3 Actuators - DIP switch 1&2 on (up), 3 down (off)
- For 4 Actuators - All DIP switches on (up)

FCB-1 Features
- Run 1 to 4 actuators in synchronous mode. (Only with Actuators with built-in feedback) This means that if one actuator is slightly slower than another, this control board will force them to run together at the same time. In addition, this feature is useful if you have an application where there is more weight or force acting on one actuator to the others, then it will also force the other faster actuators to slow down and run them all together. This is ideal for applications such as lifting doors, or a desk, etc. where un-even loading is likely. Please remember before starting to set the DIP switches at the side of the control box to the correct number of actuators first. The control box will not run correctly if the DIP switches are not correct to begin with.
- Adjust the speed of the actuators on both the extending stroke and the reversing stroke. You can set a different speed for extension and different speed for retraction
- Adjust the limit positions of the actuators (Only with Actuators with built-in feedback) – This allows you to have a starting and stopping position set independently from the built in limit switches of the actuator. Let’s say you are using a 6” Stroke Actuator but you only need 5.1” stroke, and you want the actuator to start at 0.5” from the fully retracted position, this controller lets you set the exact start and stop point.
- Works with 3 wire or 4 wire feedback signal – Hall sensor or optical sensor feedback actuators.
- Controls all actuators directly from the controller, no external switch required.
- External switch control option, can also be used with an external switch if desired.
- LCD touch screen for easy interface and operation.
Timer control options
- Time of day controller option - set the actuator(s) to open and close at a certain time of day or day of the week.
- Set up to 5 different program times - have the actuator(s) open/close up to 5 times in a 24-hr period. You can even set them for different days and different times on different days.
- Interval mode - set the actuator(s) to open and close after a certain amount of time. So, let’s say you want to open a flap for 10 mins then close it for 1 hour, and repeat that cycle continuously; this mode allows interval running, all day every day, just set it and leave.
SET-UP GUIDE
- Set the DIP switches on the side of the control to however many actuators you intend to run. The controller will not work if this is not done. There are 3 DIP switches for up to 4 Actuators. Up is on and down is off. Here are the switch positions for running 1 to 4 Actuators. Do not be concerned that there are only 4 DIP switches for running 4 actuators.
- For 1 Actuator - All DIP switches down (off)
- For 2 Actuators - DIP switch 1 on (up), 2&3 down (off)
- For 3 Actuators - DIP switch 1&2 on (up), 3 down (off)
- For 4 Actuators - All DIP switches on (up)
- Wire up the power to the control box. The controller comes with all the removable green blocks installed. Pull them off for better access to connecting the wires to each block.
- Use the wiring diagram above to help wire the power, switch and actuators correctly.
- Wire up the Actuators as shown. Remove the green blocks from the control box and wire a block to each actuator. Actuators may have different wire colors for the same connection. For example, the motor wires on some actuators are red/black, but on others blue/brown.
- The green blocks with 6 holes on them are for the actuators. The left 2 holes are for the motor on the actuators. The wiring diagram on the actuator will have a label to show +/- or maybe written as M+/M- both basically mean +(positive) and –(negative) to the motor.
- Feedback wires – The control box requires at least 3 wires for the control box to see a positional signal. Each actuator will have the labels for each wire. 5V can also be called VCC. GND is the Ground. H1 is the sensor output. Some actuators have 2 output wires which would be called Hall 1 and Hall 2 or Opt 1 and Opt 2.
- Power to the controller is via the small green block to the left of the first actuator M1. The controller takes 12-24vdc input, remember if you use a 24v DC input then the actuator(s) will also end up been powered by the same 24vdc power.
- Remove the green block and wire in power + to the left side and -ve to the right side of the green block. If you are going to use a Rocker switch in your system then you will also want to connect a second wire in this green block where the +ve wire goes. This extra +ve 12-24vdc power is going to get wired up to the rocker switch.
Note: You do not have to wire up a rocker switch. You can control the actuator from the LCD screen, but for some applications you may want a manual switch option. Follow the wiring diagram above for this.
- Once the actuator(s) are wired up and the power is connected, the control box will turn on and you will see the FIRGELLI Logo on the loading screen.
Note: If you have trouble pressing the buttons on the LCD screen you can use the end of a pen, the eraser end of a pencil, or similar sized item to accurately tap the buttons.
- Press the SYSTEM SET button to set the time and date. Here you can also turn off the buzzer if you find that annoying and also adjust the backlight of the screen.
- Note: Time must be set in 24-hr format.
- Press the ACTUATOR SET button and then then hit the CAL (calibration) button. The actuator(s) will all run an entire cycle out then back again to calibrate and, if you are using 2 or more, synchronize them.
- If the actuator(s) are not wired up correctly this is the part where you will find out. If the calibration is successful the controller will click a few times at the end of the cycle and the green light will flash.
- Note: If you did not set the DIP switches correctly the calibration process can still be performed and will still give you a green light, but when you go to run the actuators, they will not run. If that occurs, simply adjust DIP switches to the correct setting for the number of actuators you are running and then run the calibration process again.
- Once the calibration is complete, press ACTUATOR SET and then
- The controller needs to know what the stroke length of the actuator is. Read the label on the actuator and enter the correct value. So, if it’s a 6” stroke enter on the keypad 0600, the screen will read 00 INCHES. Then hit the SAVE button.
- Note: Remember even though the stroke is 6” you still have to enter a 0 before the 6, because the system allows 4 digits in total and even zero’s need to be entered.
-
ACTUATOR SET - Speed and Limit settings. Also, in the ACTUATOR SET menu you can adjust the speed (extend and retract speeds separately), as well as, move the limits for both the retracted and extended positions.
- For the limit position setting, press the LIMIT button then slide the arrows back and forth to adjust them. The bottom arrow refers to the retracted position and the top arrow refers to the extended position. They should not cross over each other.
TIMER OPERATION
INTERVAL MODE: This mode is ideal for applications where you want to open and close the actuator(s) on a set time frequency. Example: you want to extend and retract the actuator at specific intervals repeatedly, then this is the setting you would choose.
- Press TIMER OPERATION to enter the TIME SET menu, select INTERVAL MODE.
- You will be prompted to enter the “Delay Until Extend” time. The format is: hours: minutes: seconds and two digits are required for each. 2 hours would be entered as 02:00:00, 2 minutes would be 00:02:00. Press SAVE.
- You will be prompted to enter the “Delay Until Retract” Enter the length of time that will pass before the actuator(s) retract. Press SAVE.
NOTE: It’s important to remember that these times do not include the actuator(s) run time or the time delay to extend. The countdown to retract time will only begin once the actuator(s) has extended and the countdown to extend time will begin only when the actuator(s) returned back in its retracted position.
- After saving the screen goes back to the screen below.
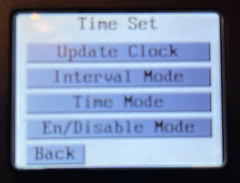
- Press the EN/DISABLE MODE button, which takes you to the next screen as shown below, to enable and start the interval program you just set.

- Select the mode you wish to enable, in this case, INTERVAL, and it will become highlighted in yellow.
- Press the BACK button twice to get to the screen below and the program will begin to run.

Note: At the top of the screen, it says “Interval 1”, this means the program is enabled and running.
TIME MODE: This mode is used to make the actuator(s) extend and retract on certain days at the specific times you set. Example: If you want the actuator(s) to extend at 10 am and retract at 4pm every Mon, Tues, Thurs, and Sat, but on Wed and Fri they extend at 11am and retract at 7pm, and on Sun they don’t run at all, this is the mode you would choose.
- Note: You can program up to 5 timers.

- Press TIMER OPERATION to enter the TIME SET menu, select TIME MODE, then TIMER 1.
- You will be prompted to enter the “Extend Time Set”. The times should be set in the 24hr clock format, and if the first digit is not required you must first enter the zero button. So, a 9am start time will be entered as 09:00:00 and a 1pm start time is entered as 13:00:00. Press
- After saving you will be prompted to enter the “Retract Time Set”. Enter the retract time, again using the 24hr format. Press SAVE.
- “Select Active Day” will appear and you will select which day(s) you would like the time setting to apply to. Active days will become highlighted in yellow. Press
- To set another timer select a different timer option (TIMER 2, TIMER 3, TIMER, 4, or TIMER 5) and repeat the steps listed above.
- Once you’ve saved the timers you wish to run, press the BACK button to return to the TIME SET MENU.
- Press the EN/DISABLE MODE button to select which timers you want to enable.

- Selected timers will be highlighted in yellow.
- Once you have selected the timers you want to use, press the BACK button twice to start running the program(s).
Note: At the top of the screen all the enabled modes will be shown. If more than one timer mode is running the display will show “Timer 1+2+3”….etc”
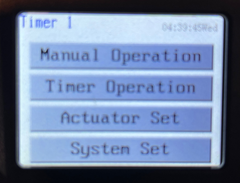
- To stop the programs running: press the TIMER OPERATION button then press EN/DISABLE MODE.
- Simply press the timer number you want to disable.
- Those highlighted in yellow are active and those not highlighted are inactive.
NOTE: When a timer is enabled you can still over-ride it by using the toggle switch (if installed) or the on-screen MANUAL OPERATION button to move the actuator. Remember that moving the actuator(s) manually will not disengage the TIME MODE programs, and it will still try to run those programs even though you are moving the actuator(s) via the switch or Manual Operation function. For this reason, it’s always best to disable any timers and/or interval modes when working on the actuator(s) or the application.
Trouble Shooting Guide
Actuator(s) running in the wrong direction: Sometimes the motor wires are wired up the wrong way around, so back could really be red and red be blue. If actuator(s) run in opposite directions then in the green blocks switch over the 2 motor wires to fix this.
One actuator does not move after it has been calibrated: Its possible that one or more wires are not connecting properly in the green connector. Unscrew each of the feedback wires in the green block, and check each wire individually. Also check that the DIP switches on the left of the box represents the correct number of actuators been used. This is very important.
All actuators calibrated fine but when running the system flashes red: This can happen because the DIP switches on the left side of the control box are not set to the correct number of actuators in use. Here is the guide again to correctly set them:
- For 1 Actuator - All DIP switches down (off)
- For 2 Actuators - DIP switch 1 on (up), 2&3 down (off)
- For 3 Actuators - DIP switch 1&2 on (up), 3 down (off)
- For 4 Actuators - All DIP switches on (up)
If you are still having problems, and have also checked the wires are correctly making contact in the green connector blocks, we recommend you unplug all the actuators and plug in just one actuator (the one you are having problems with) and try calibrating and running just the one actuator on its own. PLEASE REMEMBER, HOWEVER, to set the DIP SWITCHES to just one actuator running (all DIP switches in the down/off position) so the control box is set to run just one actuator.